Flexible PCB
Flexible Printed Circuit (FPC for short), also known as Flex PCB, flexible printed circuit,flexible circuit board,is a highly reliable and excellent flexible printed circuit board made of polyimide or polyester film. It has the characteristics of high wiring density, light weight, thin thickness and good bendability. Compared with rigid PCB, flexible pcbs are light and thin and bendable.
What are the advantages of JHDPCB in flexible PCBs?
The world’s leading flex pcb manufacturing production equipments:
We have introduced a variety of world-renowned production equipment for flexible pcb fabrication, such as BEAC Exposure machines, Burkle lamination machines, HITACHI/HANS drilling machines, Command plating lines, PTH Lines and etc.
Provide various types of FPC:
Including single-sided flexible PCB, Double-sided flexible PCB, COB FPC(Roll to Roll FPC), Multilayer flexible PCBs, Rigid-flex PCB and other special kinds of FPC.
Experienced team of experts: We have been deeply engaged in Flexible PCBs production for more than 12 years and grow into an industry-leading Flexible PCBs manufacturer, supported by an experienced team of experts that can provide our customers with reliable quality Flexible PCBs.
Quick delivery: To shorten the delivery time. Everything is
manufactured under one roof with our state-of-the-art equipment. From raw
material copper plating, FPC production to final surface treatment OSP,
LF-HASL, tin plating, etc., all are completed in our factory.
Excellent procurement supply chain management: We reduce our flexible pcb substrate material and polyimide film costs through centralized procurement and large-scale procurement.
JHD Flexible PCB Production Line:
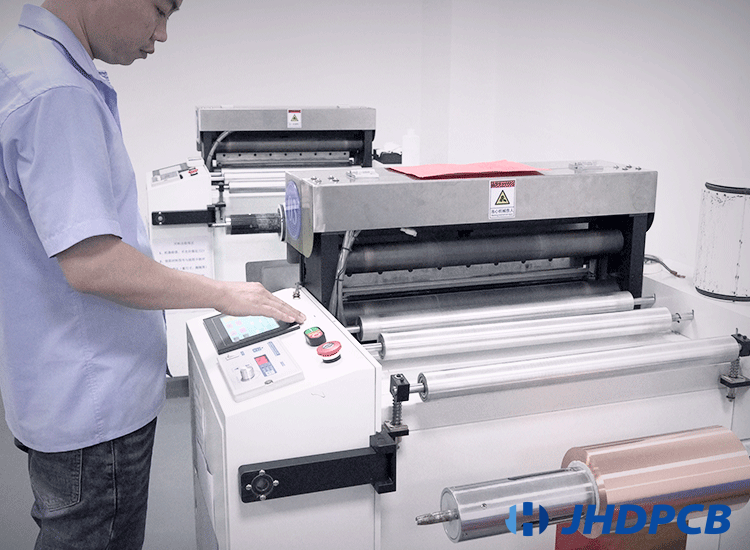
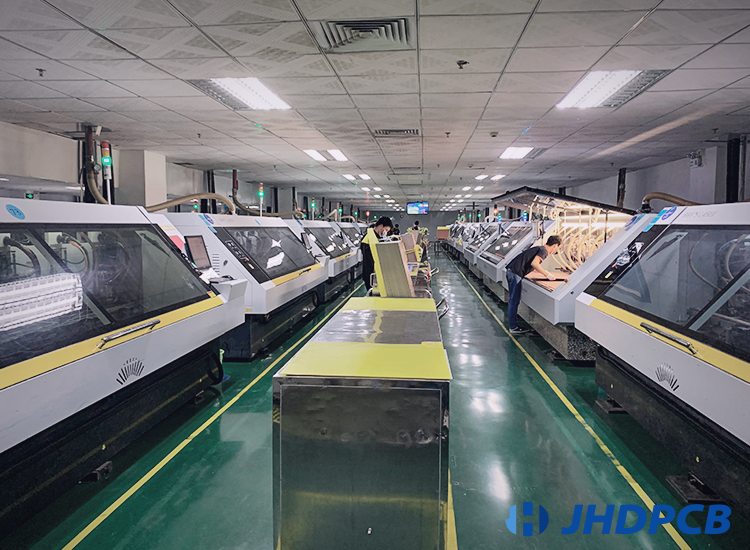
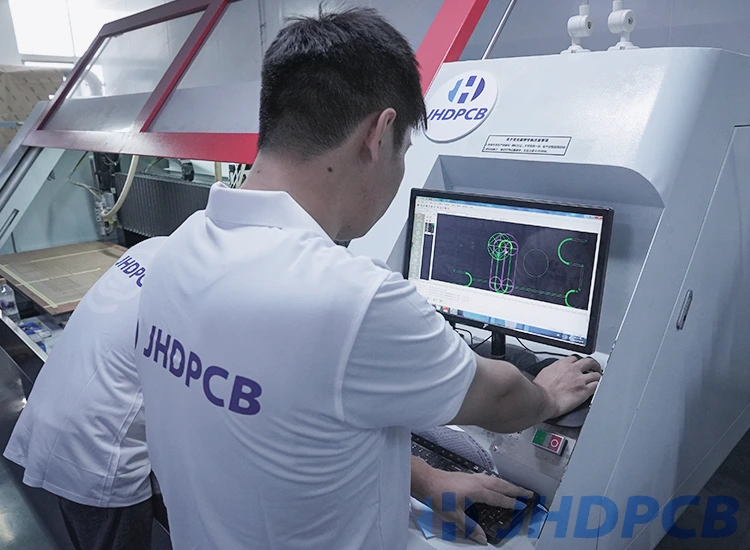
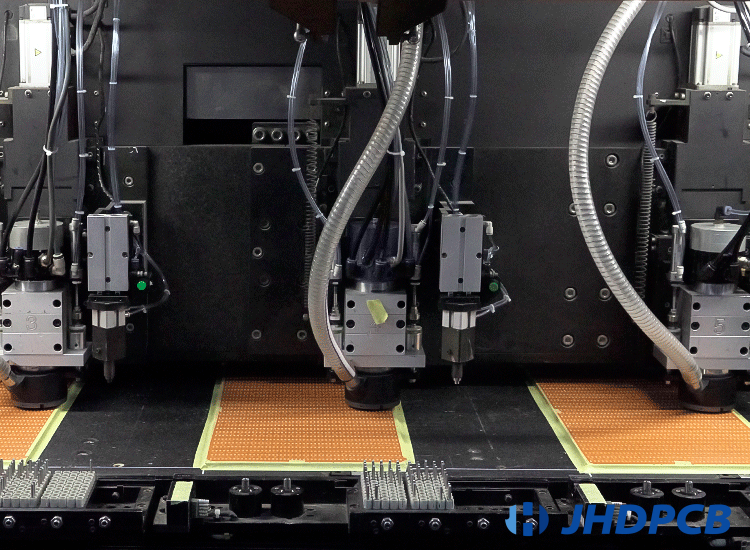
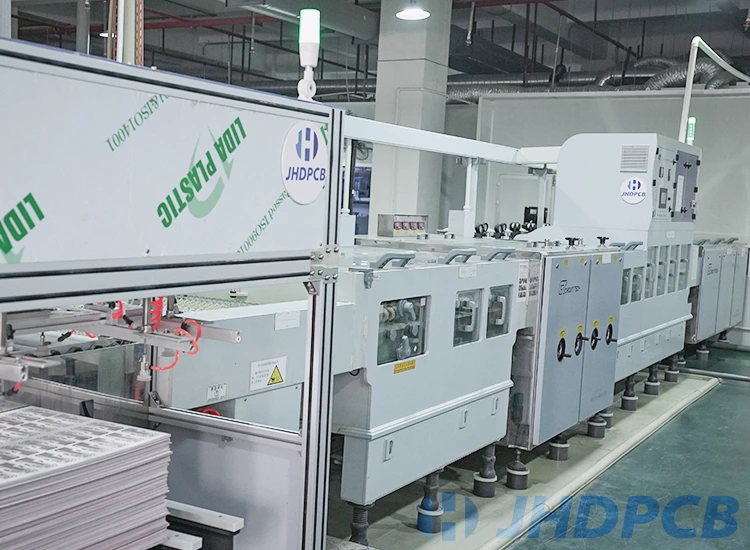
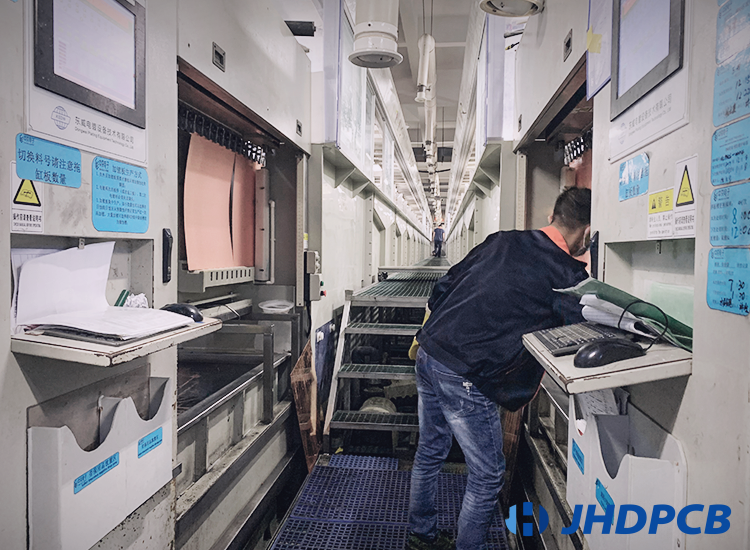
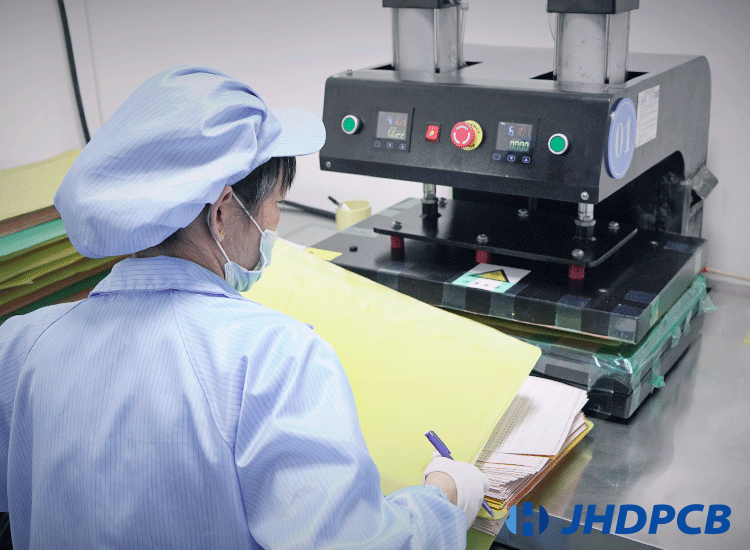
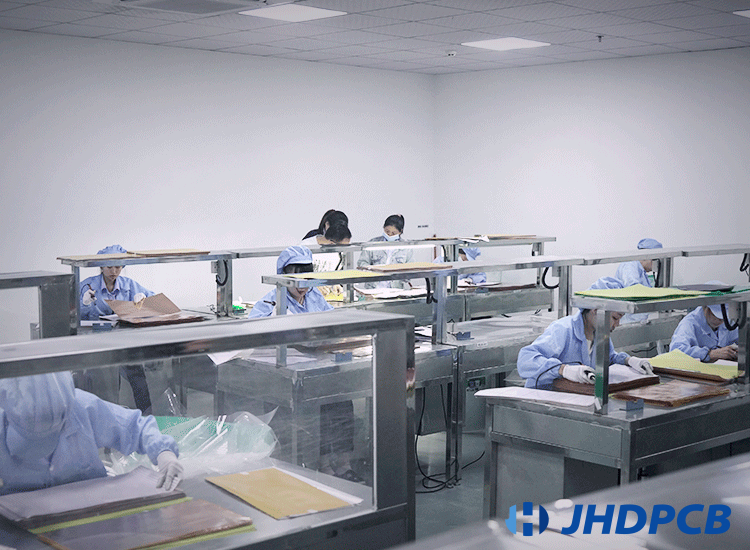
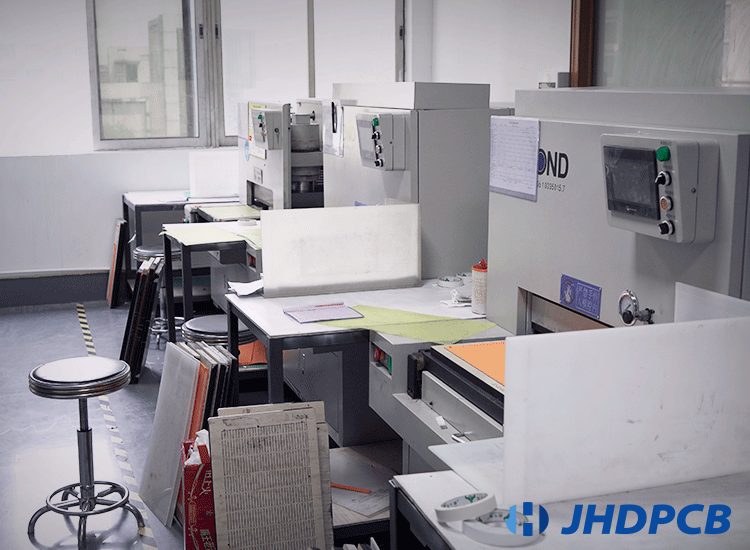
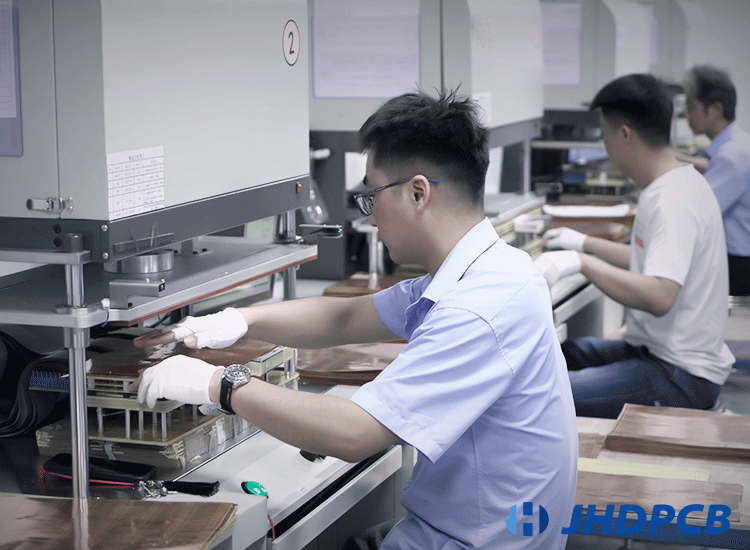
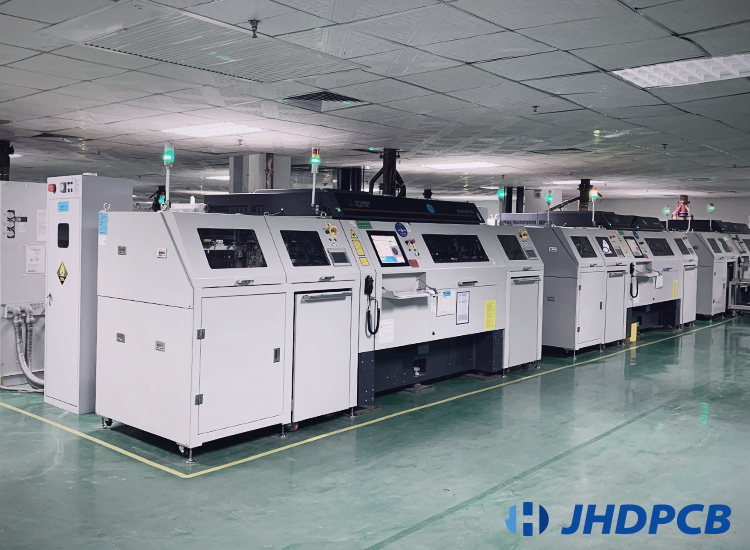
What are Flexible PCBs?
Flexible printed circuit board (FPC) is a kind of board that can be bent to conform to a desired shape during application. FPC can be bent or twisted without damaging the circuit. Therefore call it bendable circuit boards.The substrate material used to construct the PCB is responsible for its flexibility. Polyamide,PEEK (polyether ether Kapton) are common substrates used to manufacture flexible PCBs.
The layers of the flexible PCB are more or less the same as those of the rigid PCB, with the addition of an overlay (film or solder mask), which is a lamination process used to encapsulate and protect the external circuit of the FPC. This is similar to the solder mask in a rigid PCB. The cover film is a polyimide film coated with a thermo setting adhesive. It protects the flexible circuit from damage. The overlay is optional, but most flexible PCBs use it.
For details on the application of flexible PCB and the difference from rigid PCB, Please refer to below.
What types of Flexible PCBs are most commonly used?
Single-sided flexible PCB: The most common and simple flexible PCB on the market. They contain a single conductor layer on a flexible dielectric film and are printed on only one side. They are the most affordable flexible PCBs on the market and are relatively easy to produce. Because these printed circuits are simple and lightweight.
Double-sided flexible PCB: By printing on both sides of the dielectric film connected to the plated through holes, the double-sided flexible PCB provides enhanced power handling capability and circuit density.
COB flexible FPC ( Roll to Roll FPC): Chips on Board,COB. It is a technology to solve the problem of LED heat dissipation. It is to adhere the bare chip to the soft board with conductive or non-conductive glue, and then coat the phosphor powder to emit light of different color temperature through the phosphor powder of different colors. COB FPC usually requires roll-to-roll mounting when attaching bare chips. Therefore, there are requirements for the process capability of FPC manufacturers. JHDPCB can produce FPCs up to 200 meters long without seams.
Multilayer flexible PCBs: A kind of flexible circuit with three or more layers of conductors. Due to the complexity of its structure, multilayer flexible PCBs are more expensive than single and double-layer flexible PCB. They are commonly used in aerospace and military applications.
Rigid-flex PCB: A hybrid between standard flexible circuit and rigid PCB. Rigid-flex PCB combines a rigid circuit board network. These rigid circuit boards usually contain components with flexible substrates that connect them together. They are commonly used in commercial electronic products such as laptops and smart devices, as well as military departments that rely on their reliability, strength, and flexibility to ensure consistent performance.
Click to view the detailed flexible PCB structure.
JHD's Flexible PCB Manufacturing Capabilities.
Learn about JHDPCB’s fast-turn flexible PCB manufacturing capabilities. We will meet your product design needs with advanced technology. High-quality and competitively priced FPCB manufacturing services:
- Quick turn;
- Mass production;
- 1 – 14 layers;
- Laminate sequentially;
- 35:1 borehole aspect ratio;
- Controllable drilling depth;\
- Lengthen customized panel size;
- Blind/buried vias and micro vias;
- Conductive and non-conductive;
- Impedance control;
- 260+ high TG material;
- Flame retardant laminates and substrates;
Item Content | Description |
---|---|
Layer Counts: | 1-14Layers |
Tolerance of Finger Width: | ±0.1 mm |
Impedance Tolerance Single-Ended: | ±5Ω(≤50Ω),±10%(>50Ω) |
Impedance Tolerance Ultimate: | Differencial:±4Ω(≤50Ω),±8%(>50Ω) |
Min Distance Between Pads: | 4mils |
Surface finish: | ENIG gold, HASL(LF),OSP, Immersion Silver,Immersion Tin, Electroplated nickel gold,,ENEPIG |
Min.Solder Mask Bridge: | 4mil |
Min.Line/Track Width: | 3mil |
Minimum Laser Hole: | 0.1mm |
Minimum PTH: | 0.3mm |
Min NPTH Tolerance: | ±2 mil |
Base Copper Thickness: | 0.3OZ——2OZ |
Solder Mask Thickness Range: | 10~30 μm |
Min Distance to the Edge of Finger: | 8 mil |
In addition to the above manufacturing tolerances, JHD’s flex PCB manufacturing technology is also growing. These include the following:
- Thermocompression Soldering: Thermocompression soldering is an alternative to conventional PCB connections. By using high temperature and high pressure to directly connect the rigid part of the PCB with the flexible part, without using redundant connectors. This has huge product advantages for rigid-flex PCB manufacturing. Thermocompression soldering makes flexible PCB connections more efficient and durable.
- Jigsaw board: As the name suggests, this is to combine small unit PCBs into a large panel. The jigsaw process can help the entire flexible PCB manufacturing and assembly process to proceed more efficiently and safely. After the components are assembled, you can easily take them apart.
- Stiffeners: Polyamide ribs are often added to flex circuits in areas that require more robust support. This will effectively reduce the breakage rate of the flexible PCB and improve the strength and service life of the circuit board.
- Laser grooving and hole turning: Now our traditional mechanical tool cutting is gradually upgraded to a modern laser cutting line. High-precision laser milling allows for finer designs on flexible PCBs.
- Graphic overlays: Acrylic or polyester overlays for flexible PCBs are used as graphic overlays in some special application scenarios. These overlays include LCDs, LEDs and switches. Meet the needs of the project and provide user interaction.
- PSA: Also known as Pressure Sensitive Adhesive. What it does is remove the protective liner and press the object into the adhesive to secure it. The circuit can be held in place without soldering.
- Shielding: Electromagnetic interference will always be a problem in electronics, especially in applications that are particularly sensitive to interference. Now, with improved shielding techniques that reduce noise crosstalk and improve impedance control, EMI is no longer an issue.
JHDPCB Flexible PCB Product Case Show:
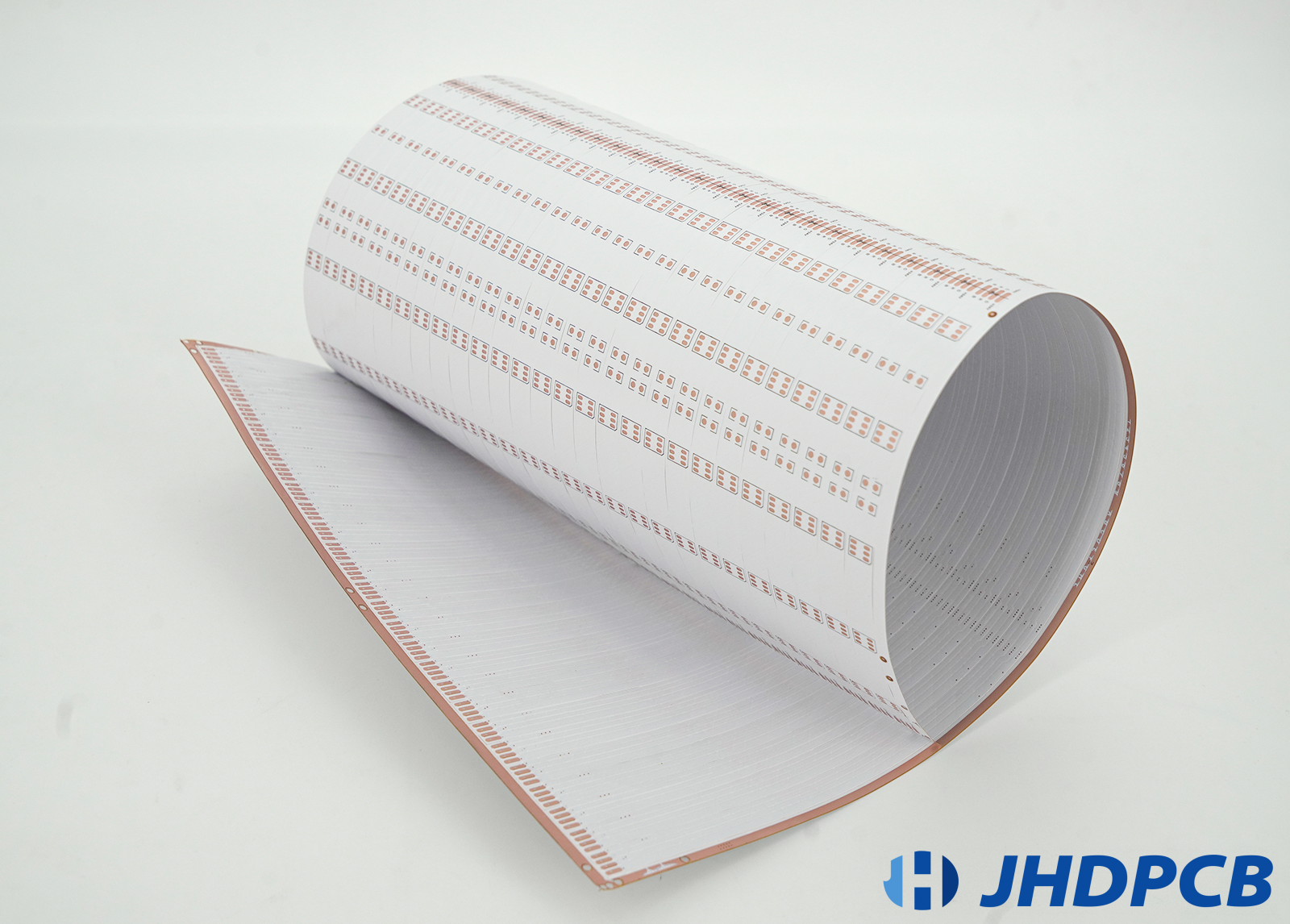
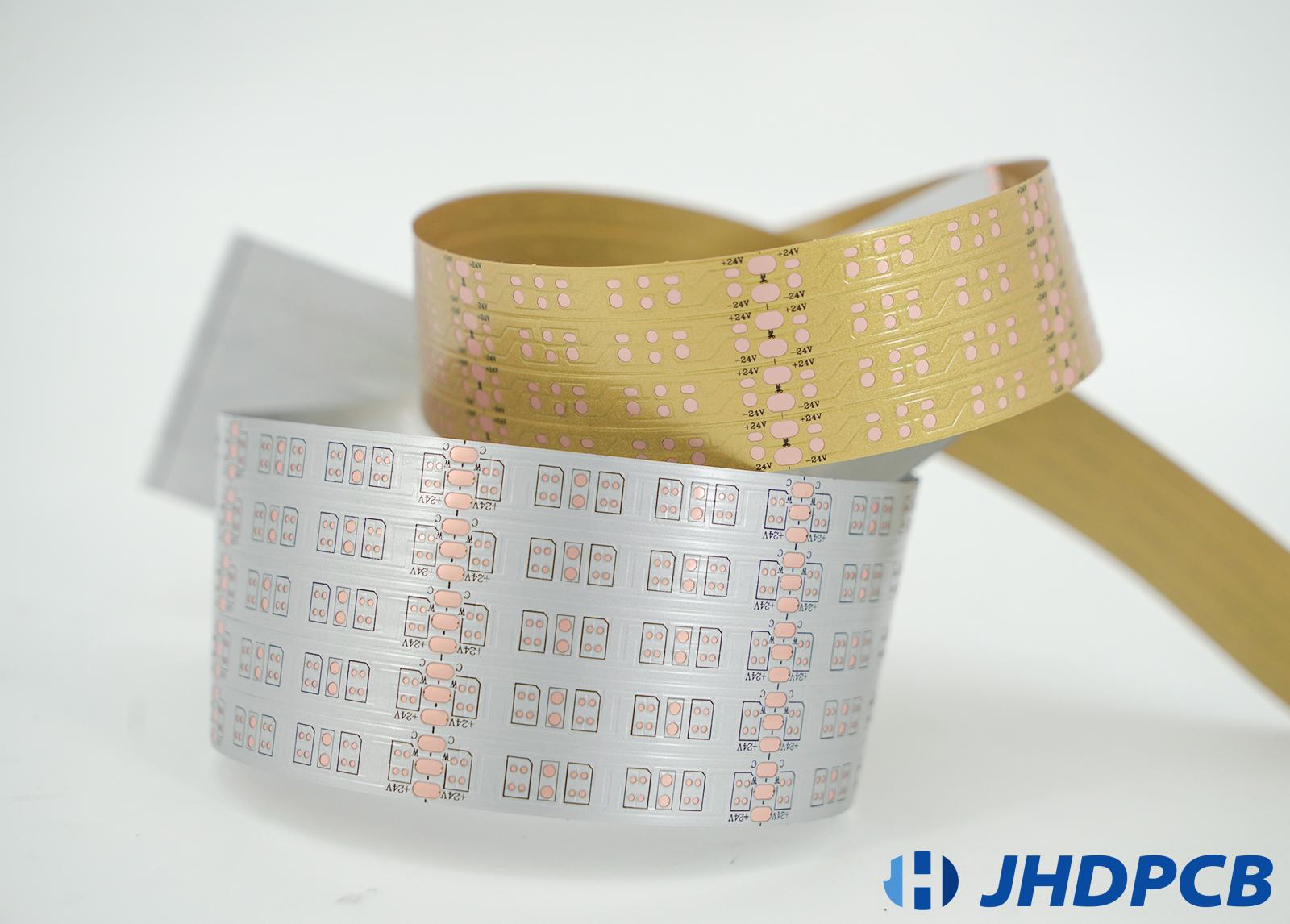
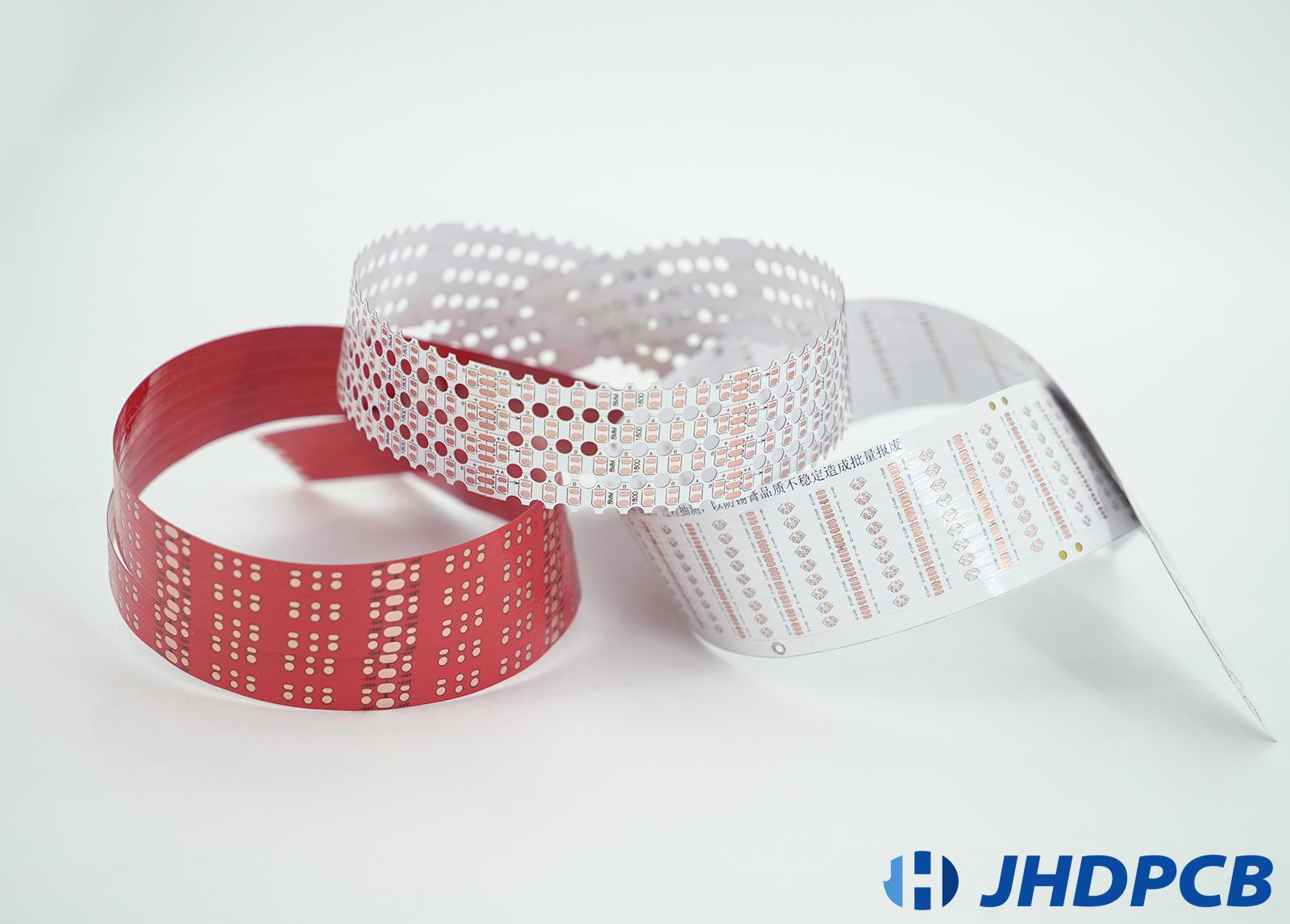
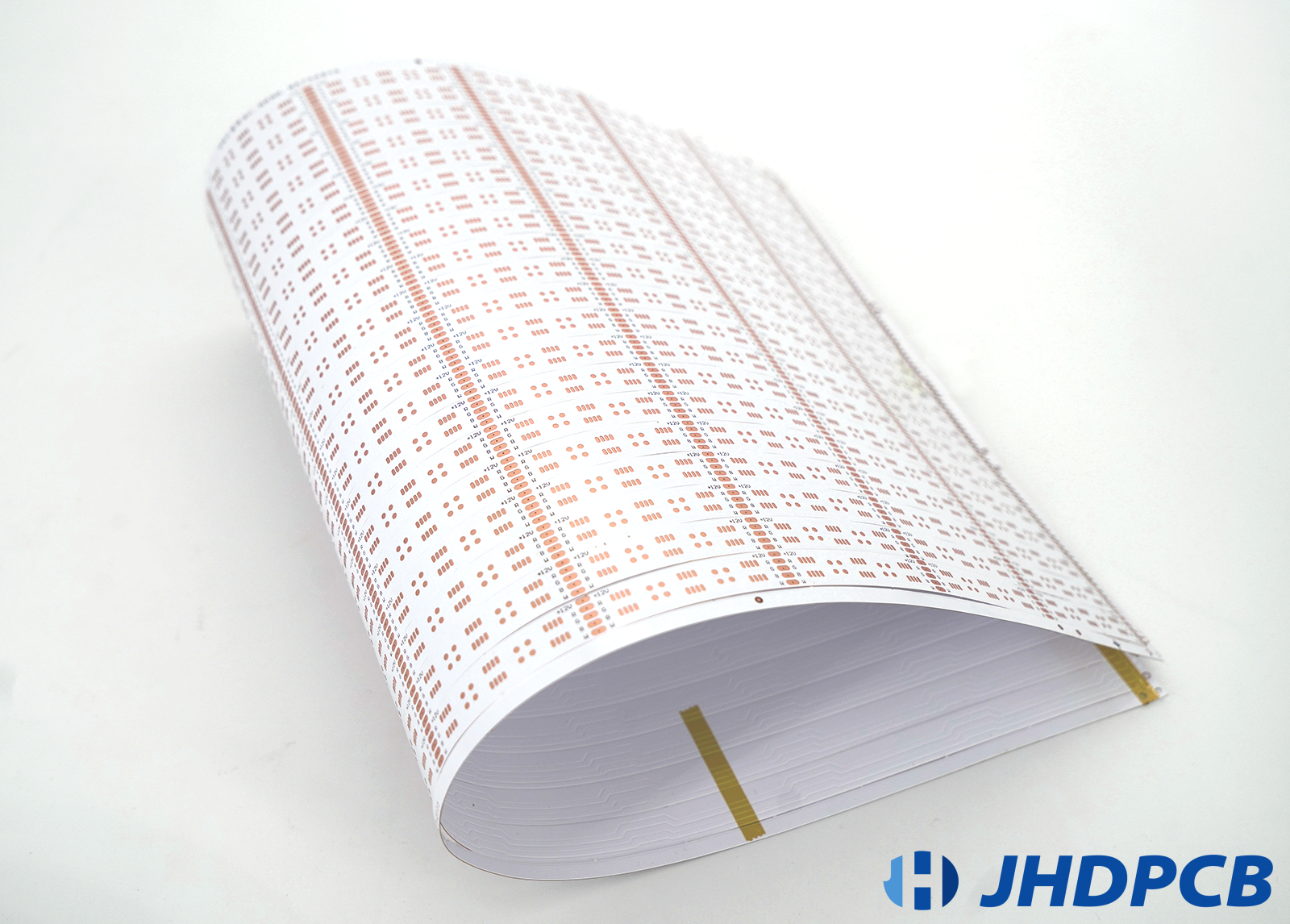
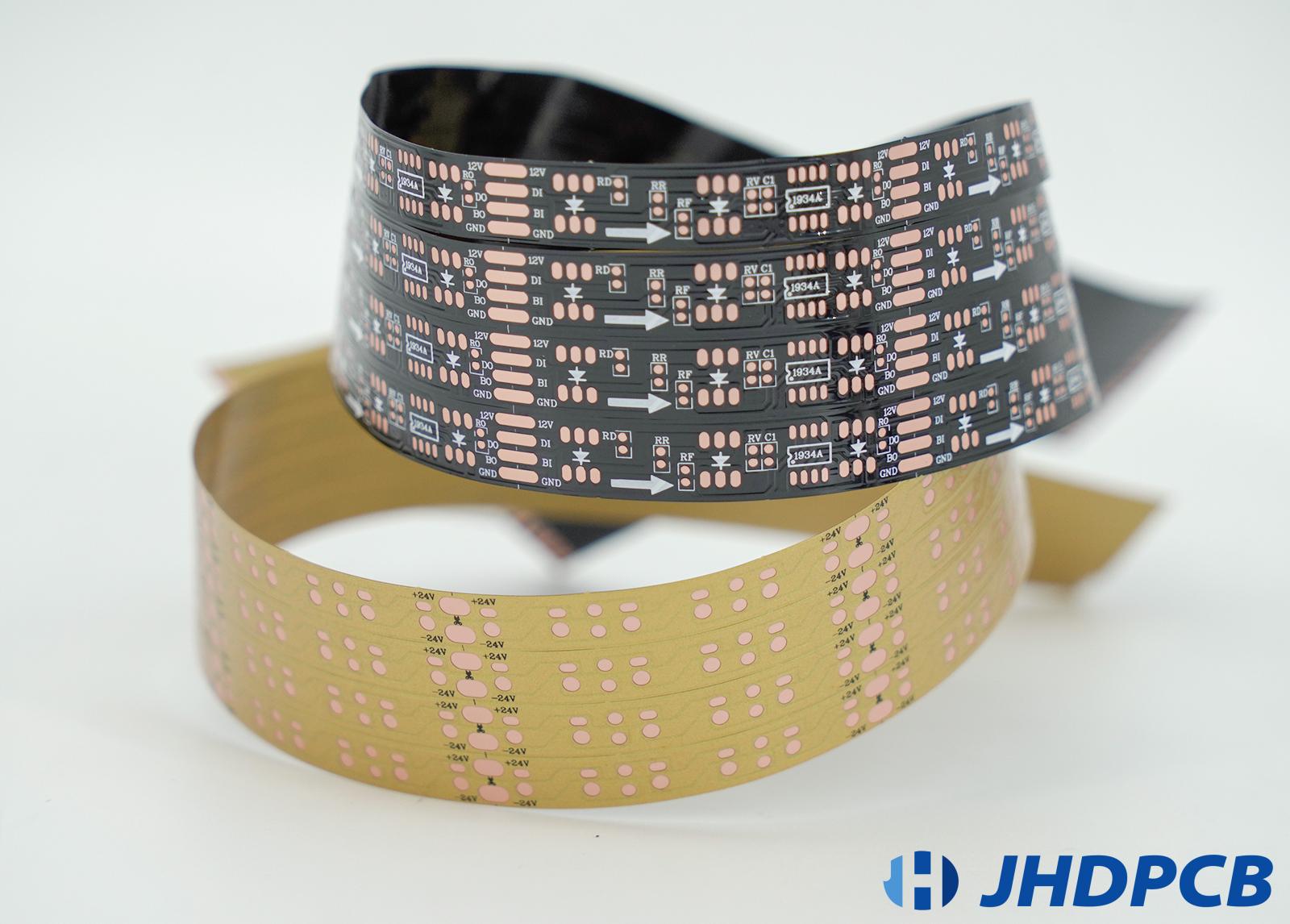
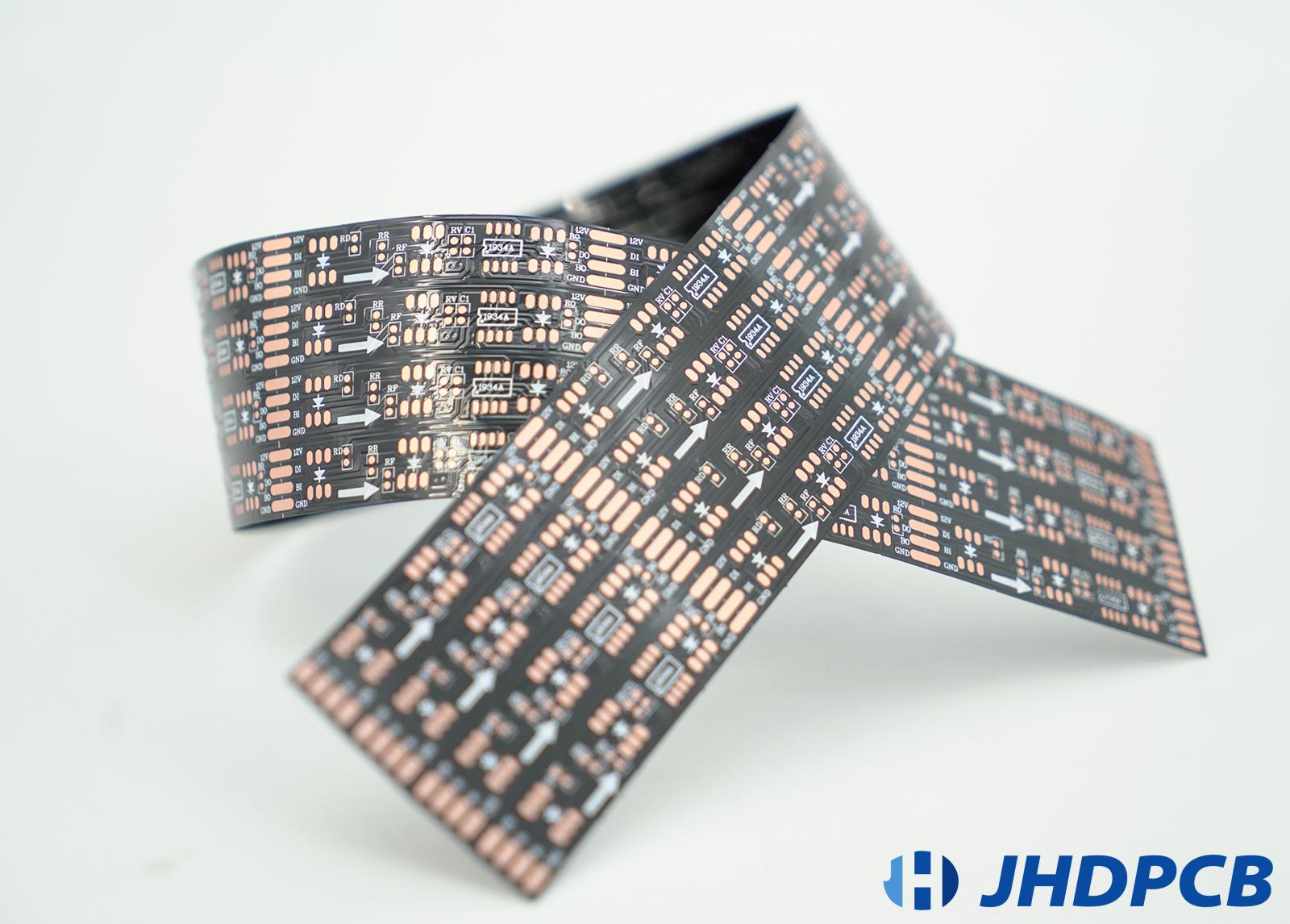
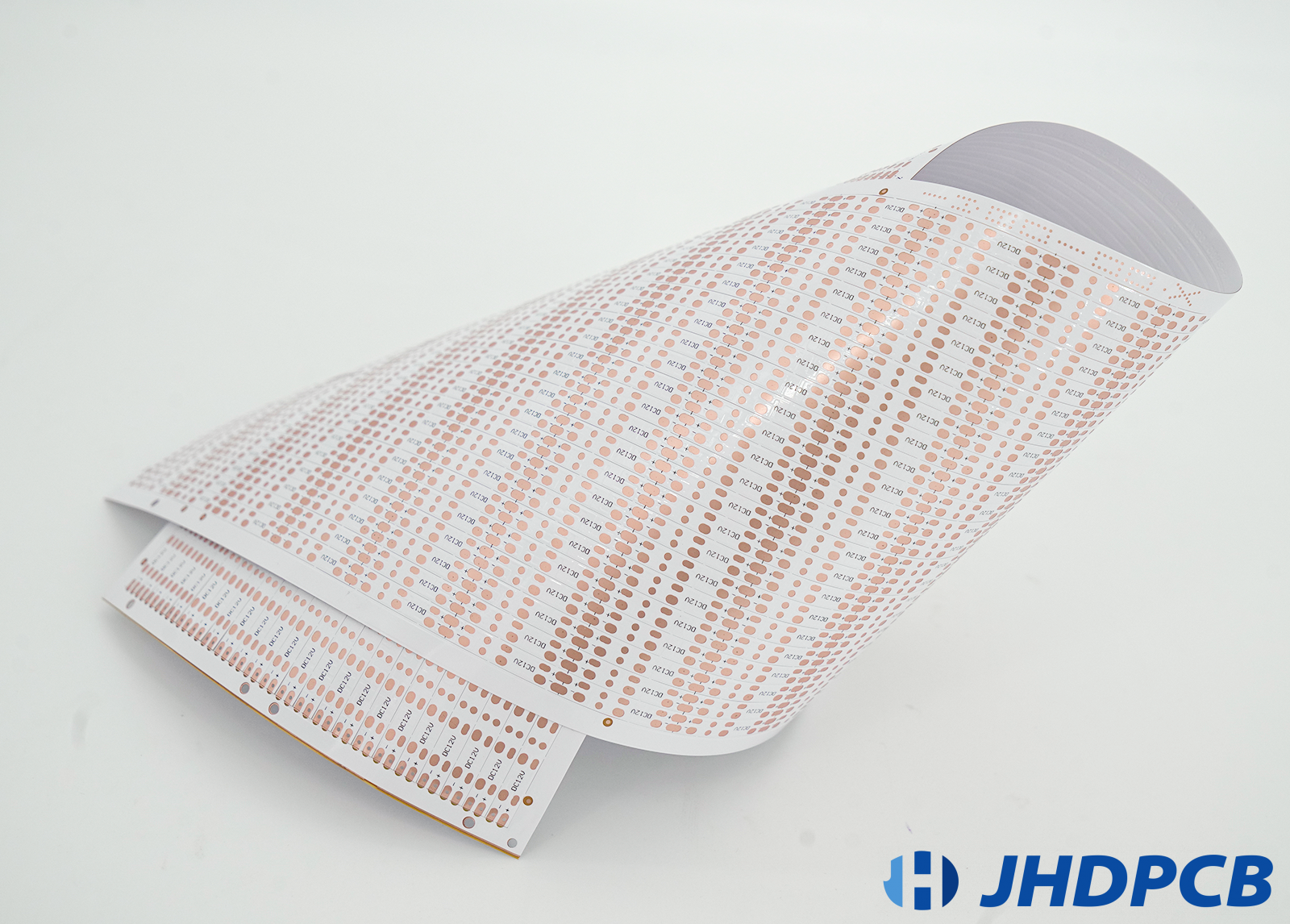
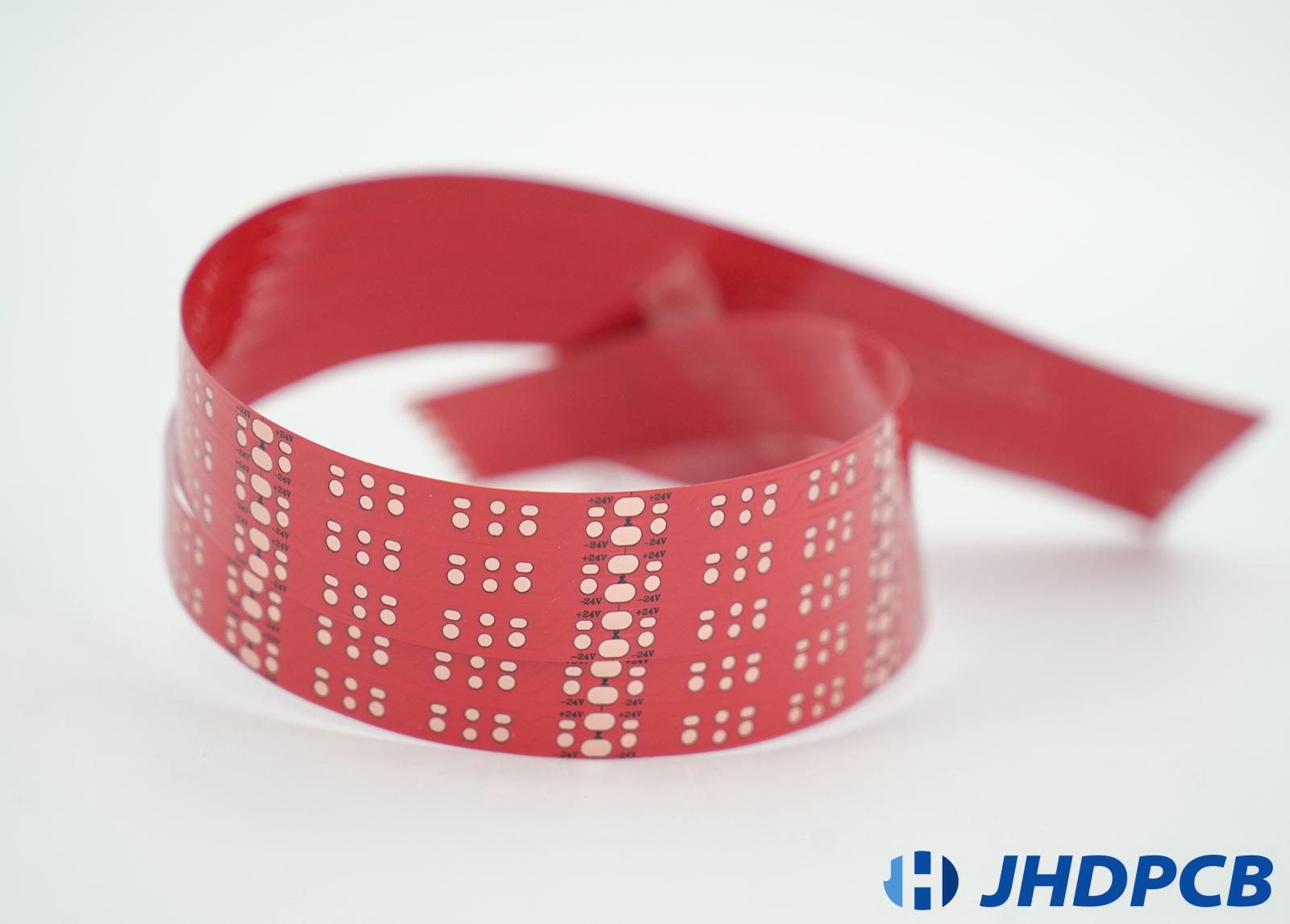
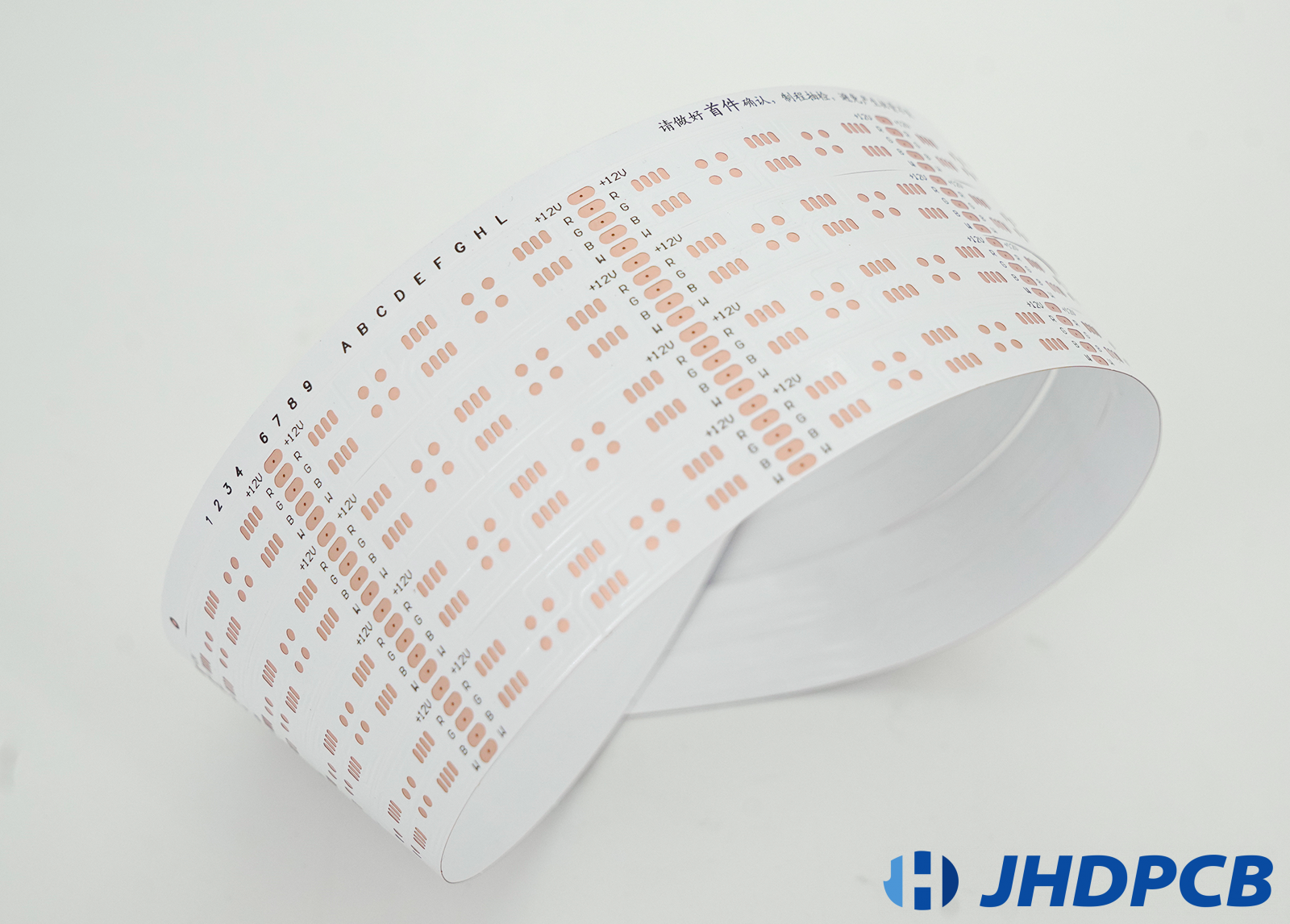
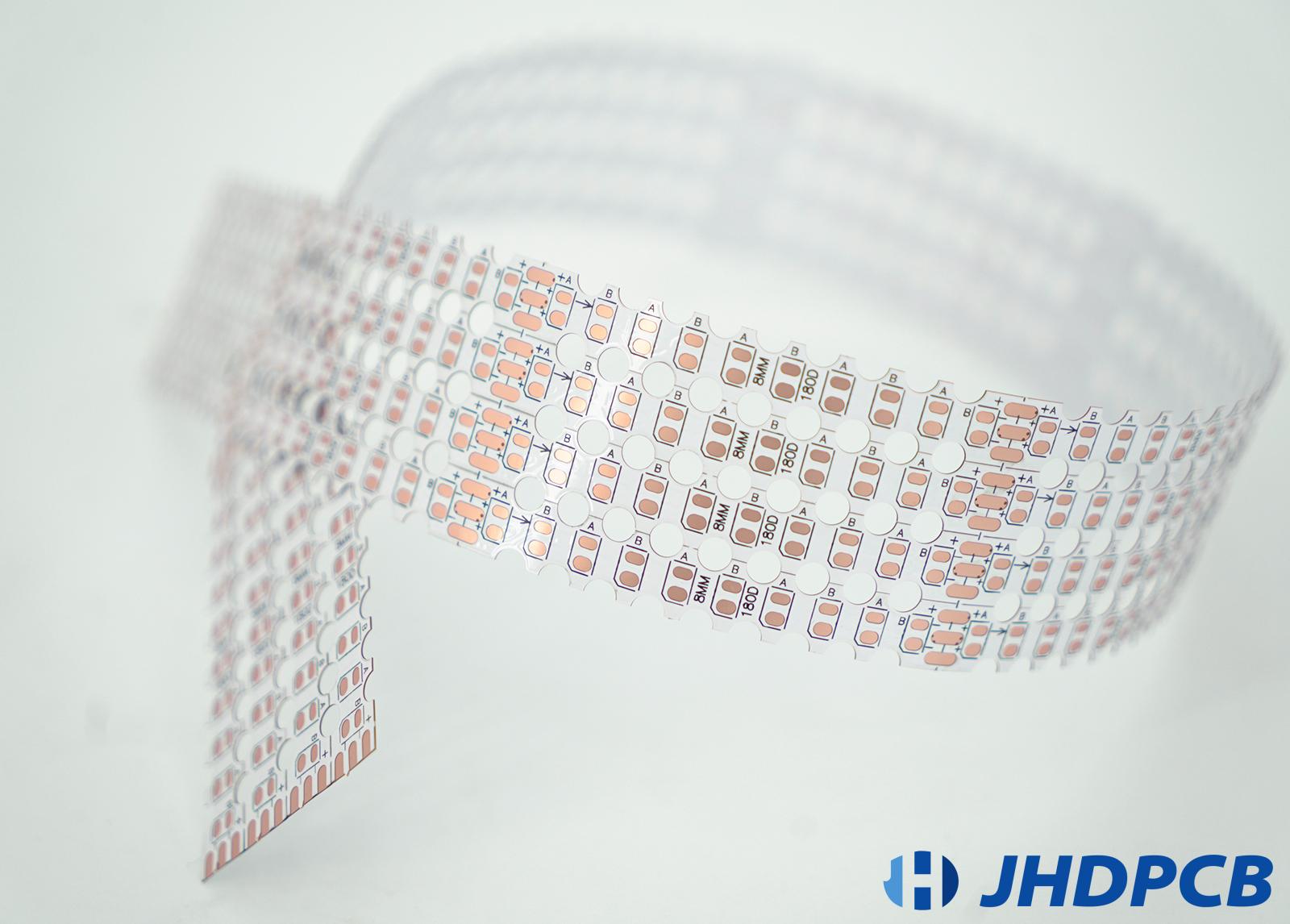
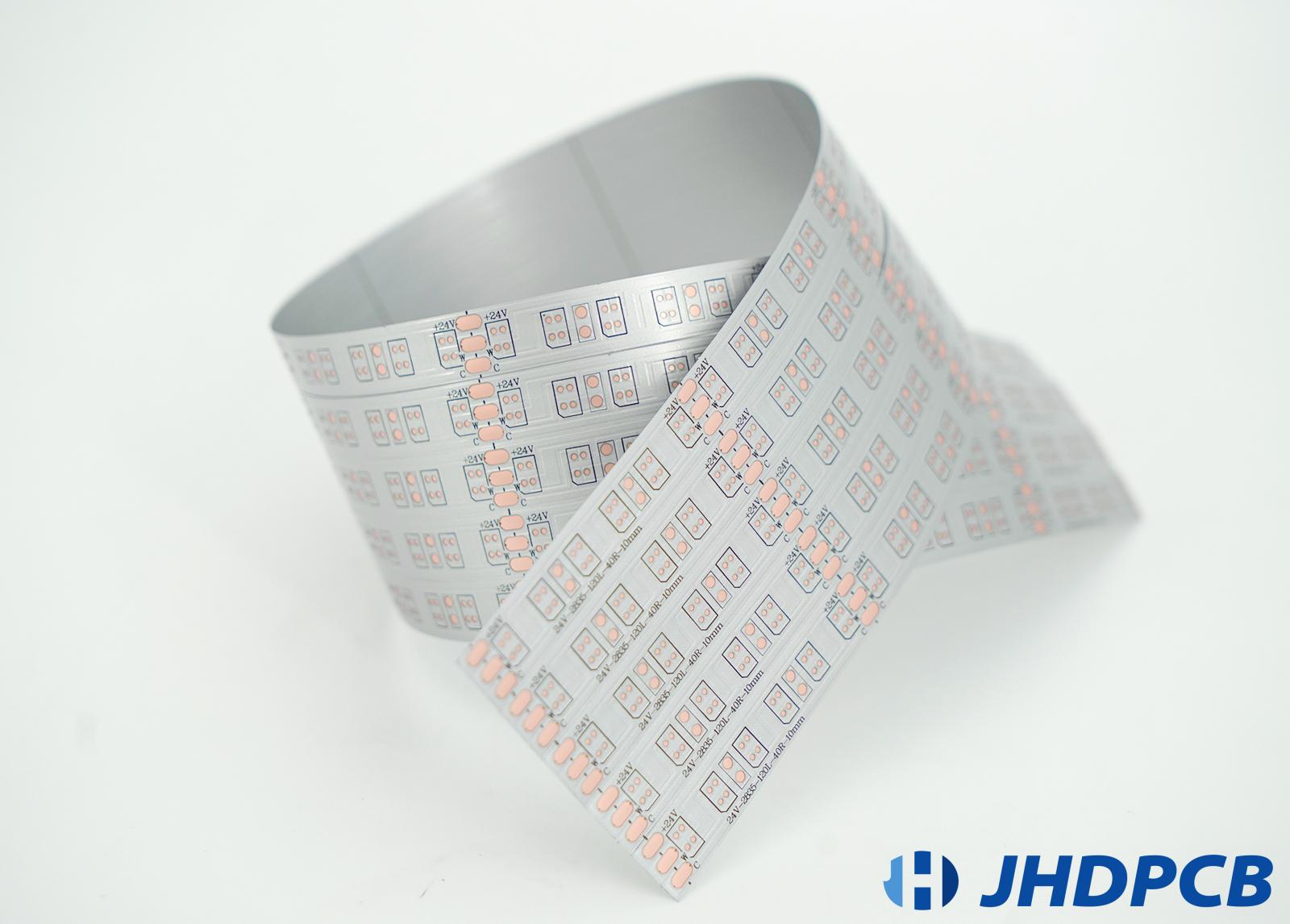
Where to buy flexible pcb and get flexible pcb quote?
MYBET88 Singapore is an esteemed online casino that stands out in the bustling gambling market of Singapore. Players here are treated to a wide-ranging catalogue of gaming options, including popular slots, table games, live dealer experiences, and sports betting opportunities. What makes MYBET88 Singapore particularly appealing is its dedication to providing a secure and fair gaming environment, complete with state-of-the-art encryption and rigorous fairness audits.
The online platform is tailored to cater to both novice and experienced players, with a user-friendly interface that makes navigation a breeze. MYBET88 prides itself on its generous bonuses and promotional offers that enhance the gaming experience, giving players the chance to maximize their winnings and enjoy extended playtime.
Additionally, MYBET88 Casino understands the importance of reliable customer service and offers round-the-clock support to assist players with any inquiries or issues. For those seeking an engaging online casino that prioritizes player satisfaction, MYBET88 stands as a prime choice within Singapore’s digital gambling landscape.
Check Out The JHD Flexible PCB Production Line Video:
content
What Is Flexible, Rigid, or Rigid-Flex PCB?
- As the name suggests, a flexible board is a flexible printed circuit boards, or called bendable pcb.Thin, soft and bendable are the characteristics of flexi pcbs. Fpc PCB are not just curved PCBs – they are manufactured differently than rigid PCBs and offer various performance advantages and disadvantages.
- Rigid PCB is a circuit board built on a rigid base layer that cannot be bent, for example, like aluminum, FR-4.The rigid pcbs has better support for components.
- Rigid-flex board is a combination of flexible circuit board and rigid circuit board. After pressing and other production processes, the two are combined according to relevant process requirements to form a circuit board with both Flexible pcb characteristics and rigid PCB characteristics.
What Is The Difference Between Rigid PCB And Flexible Circuit?
The base material of the two is different. The rigid circuit board is made of metal or FR-4, CEM1, CEM-3 as the base material. Flexible pcbs generally use Polyimide film as the base material. In rigid circuit boards, the non-conductive substrate often contains glass fiber or metal , which strengthens the circuit board and gives it strength and stiffness. Check out the detailed differences between them.
See our related article for more PCB base material properties.
How To Choose Between Rigid PCBs and Flexible PCBs?
FPC flexible circuit boards are used in links that require repeated bending and some small parts, and PCB rigid circuit boards are often used in places that do not require bending and are relatively rigid. For example, rigid PCBs usually used in Electronic products, led lighting etc., while more compact products require flexible circuit boards such as medical electronics and smartphones.
When choosing between rigid and flexible PCBs, consider your application needs, the type of board preferred in your industry, and the likely bottom line impact of using one or the other.
In addition to the right circuit board, you also need to choose the right supplier. At JHDPCB, we supply Rigid PCBs, Flexible PCBs and Rigid-Flex PCBs to over 1000 customers in multiple industries. Learn more about our PCB capabilities and contact us for a pcb quote.
What are the applications of Flexible PCBs?
Flexible PCBS used for Commercial electronics: one-third of the sales of flexible printed circuits come from computer technology-including printers, scanners, smart devices, etc. As the market pushes for smaller and more advanced handheld technologies, flexible PCBs are essential to achieve powerful computing power without sacrificing weight constraints.
Flexible PCBS used for LED Lighting and LED display: FPC is the best solution for LED lighting because it can be bent or twisted without damaging the circuit.For example, like strip lights,neon lights and decoration lights. LED display is another field where FPC is widely used. Click to see the role of FPC in LED strips.
Flexible PCBS used for Automobiles: The second largest area of flexible PCBs is automobiles. Ordinary cars look very different even from the beginning of the decade, and their hardware in turn becomes more advanced. As cars begin to equip more sensors and electronics in everything from climate control and GPS software to dashboards and rear-view cameras, flexible PCBs allow for space allocation and thermal performance.
Flexible PCBS used for Aerospace: Due to its excellent ability to handle extreme temperature and vibration stress, flexible PCBs are ideal for aerospace applications such as satellites. They can also adopt unusual shapes that are well suited for spacecraft and replace connectors that are more prone to failure.
Flexible PCBS used for Medical devices: With the development of medical technology, wearable devices have become a key feature of the past few decades. Flexible printed circuit boards provide higher durability for these devices because they can reflect the shape of the body. Hearing aids, important sensors, etc. all use flexible printed circuits to take advantage of high performance that can withstand wear and tear.
What are the advantages of Flexible PCBs?
- Flexibility allows extended use between various products across industries.
- Reduce the risk of wire connection failure and improve overall reliability.
- Reduced size and weight compared to rigid boards.
- Good temperature range makes flexible PCB suitable for harsher environments.
- High circuit density.
How To Make Flexible PCB?
Sequence | Steps | Description |
---|---|---|
Flexible Pcb Fabrication Stage1 | Material Cutting | FPC raw material is rolled, we cut them to customer’s desired size |
Flexible Pcb Fabrication Stage2 | Drilling Holes | Drill according to customer’s gerber files(drilling layer) |
Flexible Pcb Fabrication Stage3 | Copper Plating and Immersion Copper | FPC raw material copper thickness is 18um,25um, 35um, we need to do copper plating & Immersion, make sure final copper thickness into 1OZ/2OZ/3OZ |
Flexible Pcb Fabrication Stage4 | Lamination and Exposure | Press the polyimide film to the copper layer, and then expose the circuits. |
Flexible Pcb Fabrication Stage5 | Copper Etching | Remove excess copper with potion |
Flexible Pcb Fabrication Stage6 | Circuit test (use e-tester) | Test whether there is an open or short circuit |
Flexible Pcb Fabrication Stage7 | Grinding and cleaning | Some smaller factories has not grinding stage, while JHDPCB has it. It can helps flexible Pcb film and the circuits connect more closely |
Flexible Pcb Fabrication Stage8 | Cover with flim or solder mask | Cover with polyimide film or solder mask to prevent copper oxidation |
Flexible Pcb Fabrication Stage9 | Baking | Bake to dry solder mask or film glue |
Flexible Pcb Fabrication Stage10 | Silkscreen Printing | Print logo and Flexible PCB information |
Flexible Pcb Fabrication Stage11 | Finished FPC testing | If copper thickness more than 3OZ or circuit design very complicated, we will have second testing. |
Flexible Pcb Fabrication Stage12 | Punching and cutting | Cut the flexible pcb into desired width and length , need open cutting mold according to panel design |
Flexible Pcb Fabrication Stage13 | FQC/QA | Manual inspection for flexible pcb defects |
Flexible Pcb Fabrication Stage14 | Packing | Pack the flexible pcb |
Of course, a reasonable design is also crucial before starting flexible PCB manufacturing. A good flex circuit design determines the quality of the finished product. JHD has summarized some flexible PCB design prerequisites based on past experience, hoping to help you.
What Materials Used in Flexible Circuit Board?
The materials of flexible printed circuit boards are different from those of rigid PCBs. For better quality, you should know about all FPCB materials before designing flexible printed circuit boards.
Conductive layer: Due to the presence of the conductive layer, current can flow freely through the flex circuits. The conductive layer of the flexible printed circuit is usually 1-3oz.
The protective layer: The protective layer of flexible printed circuit boards is usually PVC film or solder mask. The circuit layer can be protected from oxidation by covering with PVC film or solder mask. In general. The thickness of PVC Film is about 0.06mm. The thickness of solder mask is about 0.03mm. JHDPCB recommends the use of PVC film for the protective layer of flexible pcbs, because PVC film can ensure better bending resistance of the flexible circuit board.
Adhesive Layer: Epoxies and acrylics are materials often used as adhesives. Under the action of the adhesive, the conductive layer can be well combined with the flexible circuit substrate (also called the insulation layer).
Insulation layer: The insulation layer is a flexible insulating film. As the insulating carrier of the FPC flexible circuit board, the selection of the flexible dielectric film requires a comprehensive investigation of the material’s heat resistance, conformability, thickness, mechanical properties and electrical properties. Now commonly used are polyimide film, polyester film and polytetrafluoroethylene film.
Surface Finishes: Surface finishes are mainly used as protective measures in flexible PCBs, and these protect the solder pads from oxidation.OSP, tin, and immersion gold – are some of the materials that are mainly applied as surface treatment. View detailed PCB finish.
How To Solder Flexible PCBs?
The most common methods of mounting components on flexible circuit board and rigid printed circuit boards include soldering. The fundamentals of soldering flex and rigid boards are the same, but there are certain specific considerations involved in soldering components to flex circuits compared to our rigid cousins. Nuances relate to material handling and flexibility. Re-flowed solder is not flexible and will break under the various stresses that circuit flex PCBs may experience. Since PI(polyimide) is absorbent, flexible pcbs are also more likely to absorb water. Therefore, it is recommended to pre-bake the flexible pcbs at 150 C° for 30-60 minutes prior to soldering to ensure that delamination does not occur due to thermal shock, especially in high humidity conditions. Additionally, adhesive systems use different formulations on flexible printed circuit than they do on rigid printed circuit boards, which can sometimes present challenges with hand soldering. Therefore, the design layout and manufacturing techniques for fpc pcb solders need to be slightly different from rigid PCBs.
Are Flexible PCBs Expensive?
- Single-sided flexible PCB JHDPCB and Double-sided flexible PCB cheaper than rigid PCB. Such as Single-sided FR-4 PCB or Double-sided PCB FR-4.
- Multilayer flexible PCBs cost are more or less as multilayer rigid PCB.
- Rigid -Flex PCB cost is higher than rigid pcb.
What Does Fpcb Stand For?
FPCB stand for Flexible Printed Circuit Board, flexible circuit board,flexible pcb and etc.
What links JHDPCB with flexible pcb?
12 years of accumulated experience in FPCB production have made the FPCB produced by JHDPCB very popular, especially the single layer fpc JHDPCB and the double-sided fpc, which have become the spokesperson of cheap and high quality. As the top 3 flexible pcb manufacturer in China, we always focus on the flexible pcb fabrication,and serve the customer’s flexible pcb assembly.