Medical Devices PCB manufacturing
The Role of PCBs in the Medical Devices Industry, New Technologies and New Industry-Specific Needs Challenges:
In the realm of Medical Devices, Printed Circuit Boards (PCBs) stand as the critical backbone, facilitating the seamless integration of electronic components in life-saving technologies. PCBs play a pivotal role in ensuring the reliability and precision of medical devices, from diagnostic equipment to implantable devices.
Role of PCBs: PCBs in medical devices act as the nerve center, providing the necessary connectivity for sensors, processors, and communication modules. The compact nature of modern medical devices necessitates PCBs that are not only technologically advanced but also designed for optimal space utilization.
New Technologies: Emerging technologies, such as miniaturization and flexible PCBs, are reshaping the landscape of medical device PCBs. Miniaturization allows for the creation of smaller, more portable devices, while flexible PCBs accommodate the contours of wearable medical technology, enhancing patient comfort and overall effectiveness.
Industry-Specific Challenges: However, with innovation comes challenges. Medical device PCBs must adhere to stringent safety and reliability standards. Ensuring biocompatibility, resistance to sterilization processes, and meeting regulatory requirements are paramount challenges. As devices become more complex, addressing thermal management in compact spaces and managing signal integrity become critical aspects in PCB design.
PCB development trends in the Medical Devices industry:
The evolution of PCB technology within the Medical Devices industry is dynamic, reflecting the ongoing quest for improved patient outcomes and enhanced healthcare capabilities.
- Smart Medical Devices: One prominent trend is the rise of smart medical devices that leverage advanced PCBs for data processing and connectivity. These devices, equipped with sensors and communication modules, enable real-time monitoring, data analysis, and connectivity to healthcare systems, fostering a new era of patient-centric care.
- IoMT Integration: The integration of Internet of Medical Things (IoMT) is another noteworthy trend. PCBs enable seamless connectivity between medical devices and cloud-based platforms, enhancing remote monitoring capabilities and enabling healthcare professionals to access critical patient data in real-time.
- Focus on Reliability and Durability: As medical devices become integral to patient care, there is a growing emphasis on the reliability and durability of PCBs. Ensuring long lifespan, robustness against environmental factors, and adherence to strict quality standards are becoming central considerations in PCB development for medical applications.
- Customization and Personalization: The medical field increasingly demands customized solutions. PCBs are adapting to this trend by allowing for more flexible and tailored designs, accommodating the specific needs of diverse medical devices, and contributing to the realization of personalized medicine.
In navigating these trends, PCB manufacturers in the medical industry, like us at JHDPCB, are committed to pushing the boundaries of innovation, meeting industry challenges head-on, and contributing to the advancement of life-changing medical technologies.
Medical Devices PCB Application.
- Mobile medical devices: With the advancement of PCB assembly technology, traditional wires and flexible wires have quickly become a thing of the past. In the past, traditional power sockets were usually used for plugging and unplugging wires and cords. In modern times, in order to make treatment more convenient and faster, patients can be cared for anytime and anywhere.
- Implantable medical devices: Implants have different goals under different medical conditions, so many sophisticated and complex PCB is required to run different implanted medical devices. For example, cochlear implants, implanted defibrillators, etc. all require PCB to run inside.
- Monitoring type medical devices: In the past, the integration of monitoring and recording devices was very poor, and many electronic device records lacked all types of connections. With the development of PCB, system software is connected together and has a more comprehensive interface, which promotes the pharmaceutical industry to increase the medical care of patients.
- Sterilization medical devices: Due to hospital reasons, various bacteria and viruses are prone to exist. However, in order to protect people from cross-infection, hospitals need to use some sterilization instruments for disinfection. PCB allows the sterilization instruments to run and helps the hospital’s sterilization work.
The prospect of Medical Devices PCB.
- Wide application of intelligent Medical Devices: Due to the continuous development of artificial intelligence and Internet of Things technology, smart medical devices are becoming more and more convenient and accurate, and are used by more and more hospitals. Smart medical devices allow patients to use medical products for self-examination and recovery at home, and to receive help beyond hospital assistance. Using hospital remote monitoring, preclinical treatment detection, prevention, observation and post-disease and post-operative feedback can be completed. These medical devices require highly intelligent circuit boards to realize their functions, so the wide application of smart medical devices will promote the expansion of the medical circuit board market and the requirements for PCBs to become more and more advanced and intelligent.
- 5G technology: 5G technology has now occupied our lives. It is very helpful for real-time monitoring and remote control of medical equipment. It has high speed, low latency and high reliability, which requires high-efficiency PCB to assist. Therefore, the application of 5G technology will drive the growth in demand for circuit boards.
- Medical environmental protection requirements: Nowadays, PCBs that are more environmentally friendly and have no pollution to the environment have become the main development trend. The production process of circuit boards will produce a large amount of waste water, exhaust gas and other harmful substances. Various regions are paying more and more attention to environmental protection issues, so medical circuit board technology is needed. upgrades, especially regarding the research and development of green and environmentally friendly circuit boards.
- Health awareness: As people’s attitudes towards health change, people’s awareness of health care and disease prevention is also constantly strengthening. The medical model is transforming from traditional hospitalization to personal medical products. During use, it is necessary to alleviate the cumbersome testing process and waiting during medical treatment. The problem of too long time requires more attention to the legibility of information when designing. Therefore, PCBs will need to become smaller and smaller, and at the same time, more complex circuits will be needed to make them more intelligent, high-speed and convenient.
Medical Devices PCB Application.
- Ultrasonic equipment;
- CT;
- MRI;
- Dialysis Machine;
- Digital Thermometer;
- Blood Glucose Meter;
- Sphygmomanometer;
- Heart Rate Monitor;
- Assistive hearing instruments;
- Defibrillator;
- Implanted Devices, Stents;
- Electron Emission Tomography;
- Dental Equipment;
- Oximeter;
- EKG instrument;
- EEG instrument;
- Digital X-ray equipment;
- Hematology Analyzer;
Why Choose JHD Medical Devices PCB
- Flexible PCB: Flexible PCB is the most common type of PCB found in medical equipment. Since medical devices are complex and require foldable PCBs to be placed in different places inside, the malleability of flexible PCBs makes them a good choice. When medical equipment requires foldable PCBs, flexible PCBs can be selected.
- Rigid-flex PCB: Rigid-flex PCB combines flexible PCB and rigid PCB. The FPC and rigid PCB are seamlessly pressed together through a laminating machine, and then through a series of detailed steps, the soft-hard board is finally made. These boards have greater durability, ductility and more design versatility. They are commonly found in a variety of medical devices.
- HDI PCB: HDI PCB is one of the main PCBs of modern medical device PCBs. Due to its complex processes such as fine wiring, blind via and buried via, HDI PCB is expensive, but its durability and signal transmission speed are very fast, and they even have the ability to resist electromagnetic interference and noise. Medical equipment such as CT and electrocardiograms use HDI PCBs.
- Ceramic PCB: An excellent material for PCBs in medical devices that require circuits with low thermal expansion coefficient and high thermal conductivity is ceramic PCB. Ceramic PCBs can operate at high temperatures and combine incredible high-frequency performance with strong chemical resistance.
- Automated optical inspection (AOI);
- Peel test;
- Time-domain reflectometer (TDR);
- Solderability test;
- Flying probe test;
- Time-domain reflectometer (TDR);
- Ionic contamination testing;
In order to ensure the accuracy and precision of medical equipment PCBs, JHDPCB will conduct strict tests on PCBs to ensure that the produced PCBs are of good quality.
When it comes to manufacturing PCBs for medical devices, we, at JHDPCB, understand the critical importance of using specialized materials to meet the stringent standards and requirements of the medical industry. In comparison to conventional PCB production, crafting PCBs for medical devices often necessitates the utilization of specific materials tailored to ensure compliance with the industry’s rigorous standards.
- Biocompatible Materials: In the realm of medical devices where contact with the human body is common, our PCBs incorporate biocompatible materials. This ensures that the PCBs can be safely used within the human body without eliciting adverse reactions, utilizing materials such as biocompatible polyesters or polyethers.
- High-Temperature Resistant Materials: Recognizing that medical devices may undergo high-temperature sterilization processes, our PCBs employ materials with high-temperature resistance. Materials like Polyimide (PI) or Polyether Ether Ketone (PEEK) are chosen for their ability to maintain stability under elevated temperatures.
- Biosensor-Compatible Materials: For medical device PCBs integrated with biosensors, we select materials that are compatible with biological entities. This ensures the accuracy and stability of the biosensors within the medical device.
- Flame-Retardant Materials: Understanding the need for enhanced safety in medical devices, our PCBs are crafted using materials with advanced flame-retardant properties.
- Flexible Substrates: As medical devices become more compact and portable, we incorporate flexible PCBs. These adapt to the contours of wearable medical technologies, enhancing patient comfort and overall effectiveness.
- Metal Core Materials: For medical devices requiring efficient heat dissipation, we utilize Metal Core PCBs (MCPCBs). These PCBs use metal substrates to provide superior thermal management.
- High-Frequency Materials: In instances where medical devices involve wireless communication, we opt for high-frequency PCB materials to ensure excellent signal transmission performance.
By utilizing these specialized materials, we aim to not only meet but exceed the unique demands of the medical industry. At JHDPCB, our commitment to supporting Medical Devices PCBs with these specific materials underscores our dedication to delivering products that prioritize both performance and safety.
- ISO 9000/9001: Standard for quality and reliability in the design, manufacture and testing of electronic products.
- ISO 13485: This is a quality management system (QMS) standard designed specifically for medical device manufacturers. It sets requirements for the entire product from design and development to production and post-market surveillance.
- IEC 60601: This is a series of international standards covering the safety and effectiveness of medical electrical equipment
- IEC 61010-1: These are safety rules for electrical equipment for measurement, control and laboratory use.
- IPC-A-610: This is the standard for the acceptability of electronic components, including PCBs. It covers requirements for welding, cleanliness and other aspects of production.
- FDA 21 CFR Part 820: This regulation from the U.S. Food and Drug Administration (FDA) outlines QMS requirements for medical device manufacturers, including areas such as design controls, production controls, and device labeling.
- UL 94: This is the flammability standard for materials used in electronic products. It specifies the flame retardancy and flame resistance requirements of materials.
- CFR 820: Used to verify production and quality control.
JHDPCB has many years of experience and technology accumulation in PCB manufacturing. With the advancement of today’s medical equipment, we are able to guarantee the quality of each PCB and meet relevant standards and certification requirements. Technical support and consulting services such as document inspection can also be provided to ensure that customer needs are met. If you have any needs, please feel free to contact us and we will answer your questions and ideas.
JHD Medical Devices PCB
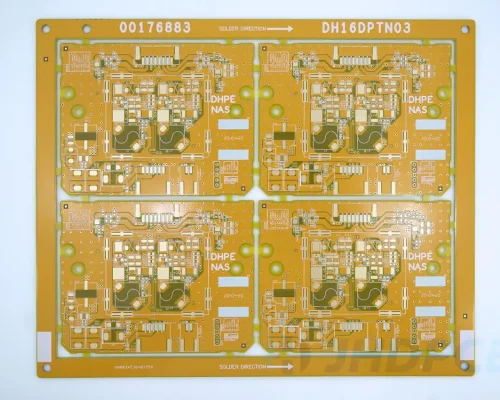
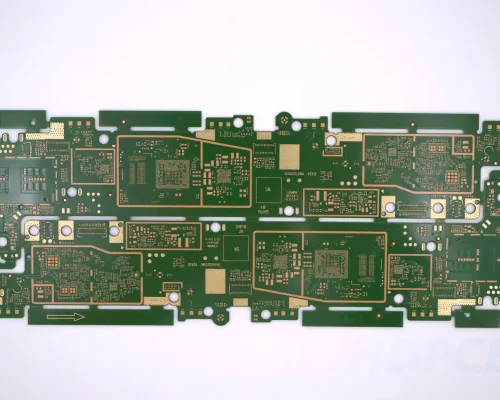
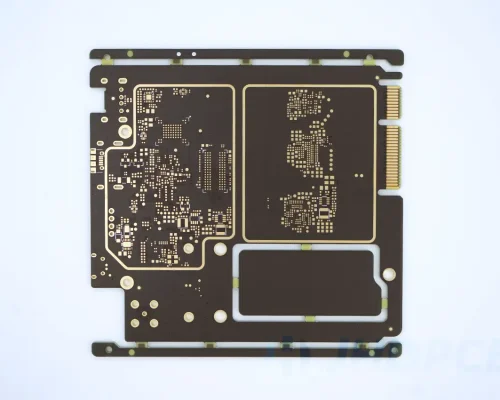
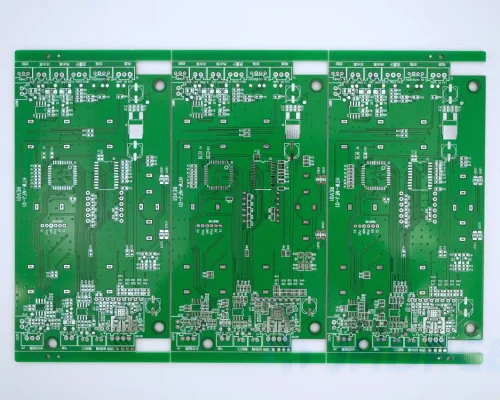