Surface finish
directory
What Is Surface Finish?
PCB Surface Finishes is the coating between the component and the bare PCB, which is one of the PCB manufacturing processes. Also called Surface Finish or surface coating. There are two basic reasons for applying it: to ensure solderability, and to protect exposed copper circuits. The PCB Surface Finishes is like a piece of cloth, helping to prevent the circuit board from being damaged by the external environment. Without this protection, the PCB may be oxidized or contaminated. Why PCB Surface Finishes is so important? That because it affects PCB reliability and PCB assembly by protecting and strengthening solder connections and copper circuits..
The Purpose Of Surface Finish.
Unlike the insulating protection of conformal coatings. Surface treatments provide PCBs with excellent solderability or electrical performance while providing some environmental protection. JHDPCB can process various Surface Finish processes according to customer needs, such as hot air leveling (HASL), hot air leveling lead-free (HASL Lead-free), organic coating (OSP), electroless nickel immersion gold (ENIG), electroless plating Nickel palladium immersion gold (ENEPIG) immersion silver, immersion tin, etc. Different types of Surface Finish have different shelf lives.
It is well known that copper is easily oxidized and deteriorated when exposed to air, which seriously affects the solderability and electrical properties of PCBs. In-circuit board manufacturing, the implementation of PCB Surface Finishes can effectively improve the reliability and shelf life of PCBA. If the surface of the circuit board is not treated, it is easy to cause soldering problems. In worse situation, the solder pads and other parts cannot be soldered.
Types and Features of PCB Surface Finishes.
There are several common types of PCB surface treatment, so how do we choose the appropriate type of surface treatment when making PCB? Firstly, we should get to know the features, values and effects of different PCB surface treatments. Then find the best fit for your project.
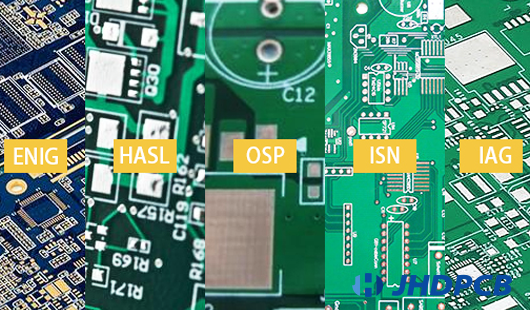
Hot air soldering level (HASL)
Hot air leveling, also known as hot air solder leveling,is a procedure in which molten tin-lead solder is covered on the surface of a PCB and leveled with heated compressed air to form a coating that resists copper oxidation and provides better solderability. A copper-tin metal compound obtained from the junction of solder and copper in hot air leveling to a thickness of approximately 1 to 2 mils.
Coat the surface of the PCB with molten tin-lead (lead and lead-free) solder, heat compressed air to level it (blow) to form a coating that is resistant to copper oxidation and has good solderability.
The general process of automated production is: micro-corrosion → preheating → fluxing → spraying tin → cleaning.
During the hot-air solder leveling process, the PCB is immersed in the molten solder. The air knife should flush the liquid solder before it solidifies to minimize solder falciform on the copper surface and prevent solder bridges.
There are two kinds of hot air levelling: vertical and horizontal. Ordinarily the horizontal type is better, and the coating of the horizontal hot air leveling is mainly smoothly.
Advantages: low cost, solid structure and excellent solderability, long shelf life, reworkable;
Disadvantages: uneven surface, prone to solder bridging, not suitable for fine-pitch components, not suitable for HDI PCB, not suitable for electroplated through holes (PTH), poor wettability;
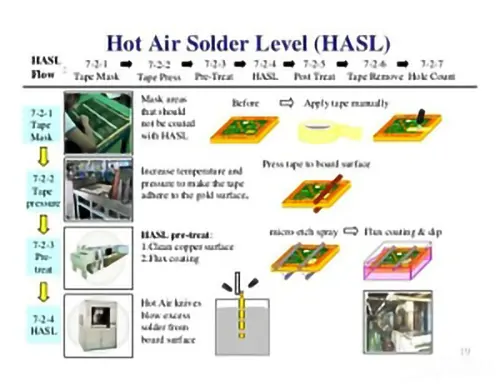
Organic Solderability Preservative (OSP)
OSP is different from other surface treatment procedures: its role is to act as a baffle layer between copper and air; General speaking, OSP is a chemistry growth of a chemical-free thin film on a bare copper ground. This layer of film has thermal shock resistance, antioxidant, and moistureproof for protecting the copper surface from rust. in a normal environment; at the same time, it must be easily removed in the subsequent welding high temperature with the scaling powder so as to do facilitate soldering.
The organic coating procedure is simple and cheap in price, with extensive use of it in the industry. The early organic coating elements are colorless crystalline and benzotriazoles with rust-proof, and the latest elements are primarily benzimidazoles. To ensure that multiple flows are possible, only one organic coating is not right on the copper surface. There must be many layers. This is why copper liquid is usually needed to chemical bathing. After the first layer is applied, the coating adsorbs the copper; then the organic coating molecules of the second layer attach to the copper until more or even hundreds of organic coating molecules accumulated on the copper surface.
The surface finish of OSP is also non-conductive. It is RoHS Conformance and has good solderability.
The general process flow is: degreasing→micro-etching→pickling→pure water cleaning→organic coating→cleaning. which is much easier than other treatment processes.
Advantages: low cost, simple manufacturing process, lead-free, smooth surface, suitable for SMT assembly, and repairable;
Disadvantages: highly sensitive, not suitable for PTH, difficult to measure thickness, limited shelf life, non-conductive
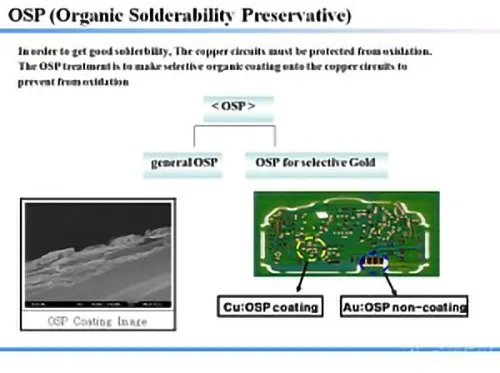
Electroless Nickel Immersion Gold (ENIG)
Electroless nickel/immersion gold, or ENIG for short, also known as nickel-gold, immersion nickel-gold or electroless nickel-gold plating, is to replace palladium on the copper surface by chemical reaction, and then chemically coat a layer of nickel-phosphorus alloy on the palladium core, and then replace it by replacing palladium on the copper surface. The reaction coats the nickel with a layer of gold. There are two processes for the immersion gold of nickel and gold, the substitution semi-replacement and the semi-reduction mixed plating.
Electroless nickel gold is mainly used for surface treatment of circuit boards. Used to protect the copper not being oxidized or corroded on the surface of the PCB board. It can also be used for soldering and contacts ,like buttons, gold fingers on memory sticks, etc.
ENIG surface treatment is a nickel-containing double-layer metal coating, which can protect the PCB for a long time and act as an anti-rust barrier. It can play a role in the long-term use of the PCB and obtain good electrical properties. At the same time, it also has feature of environmental resistance but other surface treatments without it. It can be used as a protective barrier for copper circuits and the surface of soldering components.
The general process flow is pickling→micro-etching→pre-dipping→activation→electroless nickel plating→chemical immersion.
Advantages: Hard and durable, with longer shelf life,excellent weldability, lead-free and RoHS certification, smooth surface, better anti-corrosion and simple procedure mechanism,as well as high temperature resistance.
Disadvantages: with connection errors and cracks on the surface, a little difficult to rework,higher-cost.
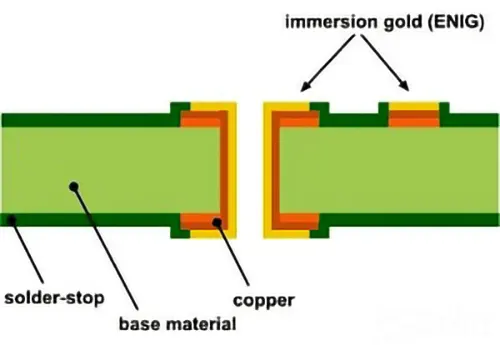
Immersion Silver (IAg)
Immersion silver is the surface finish of the immersion silver plated on the board. The characteristics of the immersion silver process are between OSP and ENIG. Immersion silver not wearing heavy armor to the PCB. Even if uncovered to high temperature, humidness and contamination, it can provide excellent electrical functioning and maintain excellent solderability, but it will lose its lustre. Immersion silver does not have all the better physical force required by ENIG as there is no nickel below the silver layer.
Immersion silver is a hypallage response, which is almost a sub-micron coating of pure silver. But the immersion silver procedure also involves some organic material, mainly to avoid silver erosion and get rid of the problem of silver migration. It is always difficult to estimate this thin layer of organic material. The survey displayed that the the organism weight was no more than 1%.
Silver is the most electroconductive material at the moment. Immersion silver is fit for riskless PCB assembly procedures, especially for high-speed print circuit board appliances.
Advantages: excellent solderability, high-cost performance, flatness, high stability, and high conductivity;
Disadvantages: silver chips, loss of luster, creep corrosion;
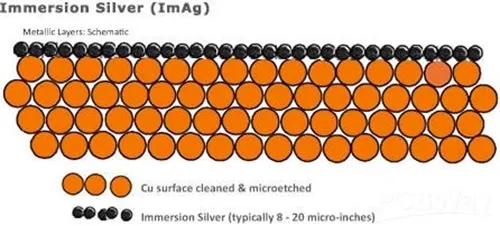
Immersion Tin (ISn)
Immersion tin refers to plating a layer of immersion tin on copper circuits. The immersion tin procedures can form flattened copper-tin chemical compounds with excellent solderability, such as hot air leveling(HAL), but there is no flatness problem. there is also no electroless nickel plating/dipping Diffusion between gold and metal; it’s just that the immersion tin plate can’t be stored for too long.
This surface finish is ideal for SMT applications, BGA and fine pitch parts.
Since all solders with material tin, the tin layer can be matched with any kind of solder. Looking from this angle, the immersion tin process is very promising. However, in the past, tin beard were available after the immersion tin procedure, and the moving of tin beard and tin during the soldering procedure would result in reliability problems, thus limiting the use of the tin immersion procedure. Later, organic addition agent were added to the tin dipping solution for making the tin layer granular structure, which conquers the previous problems and has excellent solderability and thermal stability.
Advantages: lead-free and RoHS compliant, smooth surface, high cost performance, high reliability;
Disadvantages: high sensitivity during processing, exposed tin is easy to corrode, and the shelf life is short (about six months), expensive, prone to surface cracks and connection errors, not easy to rework.
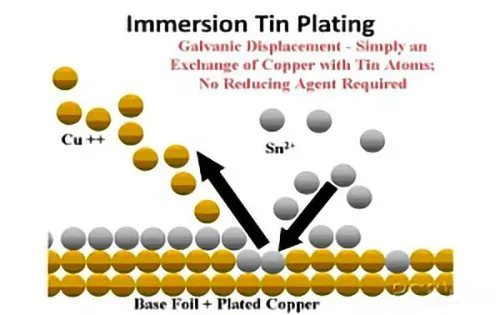
How to Choose PCB Surface Finishes?
PCB finish helps protect copper circuits from corrosion. It also provides a solderable surface for the components of the PCB. There are many factors to consider when selecting a surface treatment process, including:
Components used, Expected output, Requirements for durability, Environmental impact, Cost.
Actual Solderability Comparison: Electroplating nickel gold> HASL > OSP > ENIG >Immersion silver >Immersion tin.
Cost comparison: Electroplating nickel gold > ENIG > Immersion silver> Immersion tin > HASL > OSP.
For the complete PCB Surface Finishes process, please refer to the “PCB Surface Treatment Guide“
All Surface Finish have advantages and disadvantages. It depends on your PCB design, function, storage time, process method and application area to choose the right type. If you are still confused about the options, please contact us for more information before placing your order. Our professional business personnel will provide customized services for your project according to your needs.